When it comes to protecting your vehicle's paint, ceramic coatings have become a go-to choice for many car enthusiasts. But how much do you know about what it takes to get that perfect shine and long-lasting protection? You might think it's just a simple process of applying a liquid layer, but there's a lot more happening behind the scenes. Understanding the science of curing times is crucial for ensuring your coating performs its best over time. In this article, we'll break down the basics of ceramic coatings and explore the intricacies of their curing process. Whether you're a first-timer or have applied coatings before, there’s something valuable here for everyone eager to make their vehicle look its best!
The science behind
ceramic coating cure times involves a chemical reaction known as cross-linking, where the coating forms strong bonds with the vehicle's surface. Optimal curing typically spans 7 to 14 days, depending on environmental conditions such as temperature and humidity, which are crucial for achieving maximum durability and protection against damage.
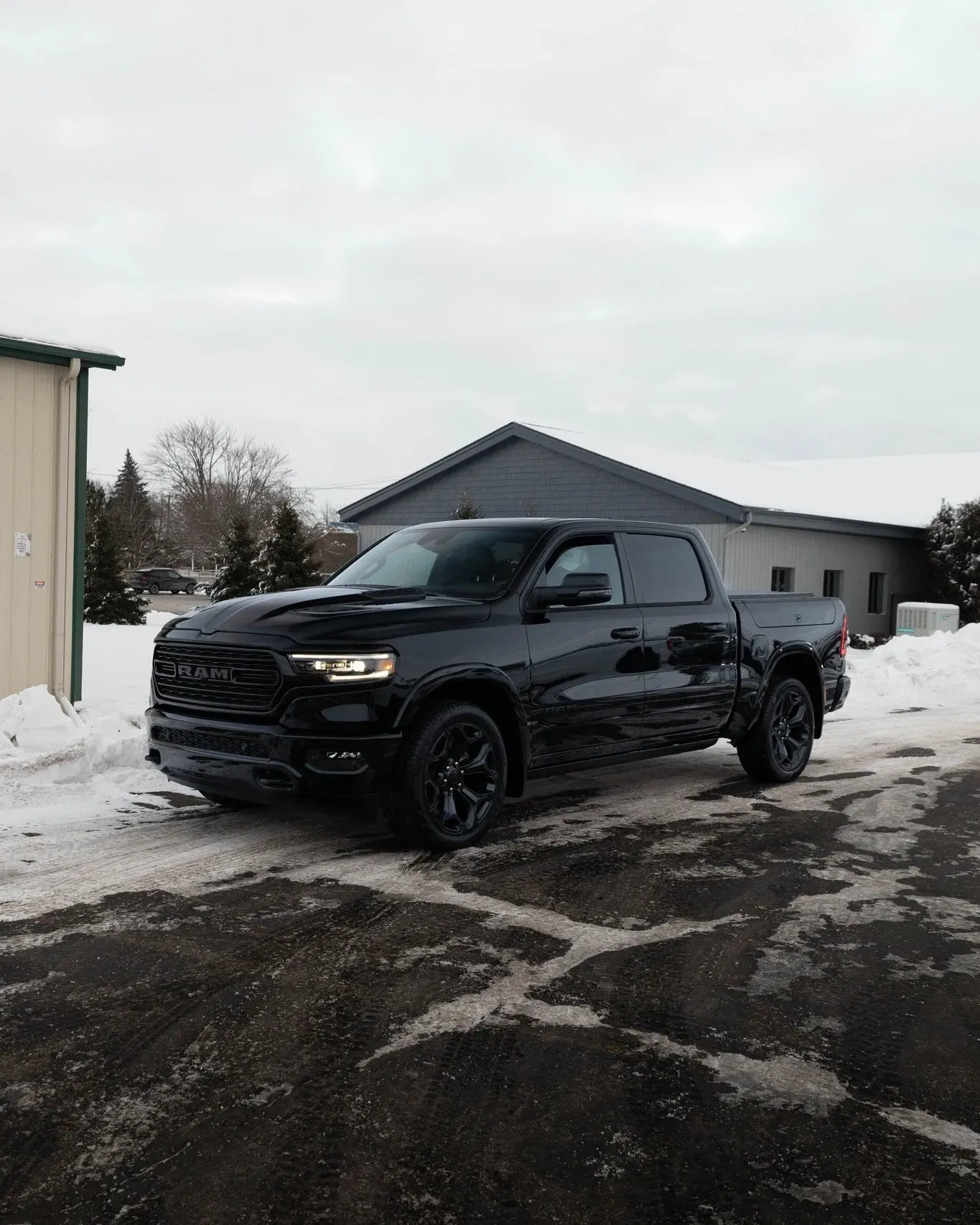
Basics of Ceramic Coatings
At its core, a ceramic coating is not just a protective layer; it's a sophisticated blend of science and artistry. Made primarily of silica (SiO2), this liquid polymer is meticulously applied to a vehicle's surface by hand. When it adheres to the factory paint, it doesn't just sit on top — it chemically bonds with the paint, forming a robust shield that defends against everyday wear and tear.
Properties That Set Ceramic Coatings Apart
What makes ceramic coatings different from traditional waxes and sealants? The primary distinction lies in how they interact with your car's paint. Traditional products merely coat the surface, offering minimal protection; however, ceramic coatings create a semi-permanent bond that deeply embeds within the paint layers. This characteristic ensures significantly longer-lasting protection—something many car enthusiasts highly value.
Imagine treating your car’s exterior like skin; while basic waxing merely puts on sunscreen, a ceramic coating is akin to applying advanced anti-aging cream. It actively fights off the corrosion that the environment can wreak upon your vehicle’s finish.
Surface Characteristics
Moreover, one of the most impressive attributes of ceramic coatings is their hydrophobic properties. This means that water beads off surfaces rather than creating unsightly spots or stains. For vehicle owners, this feature not only enhances aesthetic appeal but also reduces the frequency of necessary washes. Research states that cars treated with ceramic coatings can maintain their pristine appearance far longer than untreated vehicles.
With our exploration of these remarkable protective features behind us, it’s time to investigate the complexities involved in achieving optimal curing times—an aspect that greatly influences both performance and longevity.
Understanding the Curing Process
The curing process transforms ceramic coatings from a liquid state into a robust, protective layer. This isn't just a simple drying of the surface; it’s an intricate chemical transformation that ensures the coating adheres effectively to your vehicle's paint. Hence, understanding each stage is vital for optimizing both application and performance.
Chemical Bonding
At the core of this transformation lies chemical bonding. During this phase, intricate reactions occur that form strong bonds between the coating and the vehicle’s surface. This interplay dictates how well the protective layer will perform against elements such as UV rays, water spots, and scratches. Poorly formed bonds can lead to premature wear and tear, negating the very benefits ceramic coatings provide.
Stage I: Initial Drying
The first stage, known as initial drying, occurs fairly quickly after application, within a few hours to a day. Here, the solvents within the coating evaporate. It’s interesting to note that during this initial phase, you may find that the coating feels tacky. This stickiness is entirely normal; however, it's essential to keep your vehicle dry and free of contaminants during this time. If water or dirt clings to the surface while it’s still tacky, it could disrupt the forming bonds, leading to imperfections in your final protection layer.
Stage II: Cross-Linking
Moving on to what many experts consider the most critical part of curing—the cross-linking phase. Here, the coating undergoes transformational chemistry as molecules bond together in a cross-linked manner; think of it as weaving a sturdy fabric from individual threads. This process takes between 7 to 14 days and dictates how durable your coating will be.
The strength derived from effective cross-linking leads to impressive benefits such as heightened resistance to scratching—research suggests that properly cured coatings resist damage 30% more than those improperly cured. This stage's duration varies significantly based on environmental factors like temperature and humidity. Optimal conditions consist of temperatures between 60°F and 80°F (15°C - 27°C) with humidity levels below 50%. If these conditions aren’t met, you might find yourself extending that curing timeline further than expected.
Factors Influencing Curing Duration
One major factor that can significantly affect curing duration is the type of ceramic coating used. Different brands and products come with their unique formulations that inherently influence how quickly they can cure. For instance, premium professional-grade coatings from trusted names like Gtechniq or CarPro tend to include advanced chemical compositions, which may expedite curing times compared to more basic consumer-grade options. Understanding its specific characteristics can help set realistic expectations for performance.
However, while the type of coating is important, it’s equally essential to consider environmental conditions.
Environmental factors such as temperature, humidity, and air circulation are pivotal during the curing process. Warmer temperatures generally accelerate chemical reactions, effectively speeding up the curing time. Ideally, applying ceramic coatings in a controlled environment where temperatures hover around 70°F (21°C) is recommended. Conversely, high humidity can be problematic; moisture can hinder the bonding process between the vehicle's surface and the coating itself, resulting in longer cure times or even compromised adhesion. Maintaining a dry and well-ventilated area while applying your coating can dramatically improve its overall effectiveness.
It’s also worth noting that direct sunlight exposure during application may cause the product to dry too quickly on the surface without achieving complete bond formation, leading to patches that may not provide full protection later on.
Understanding these elements allows you to take proactive steps towards ensuring a successful ceramic coating application.
Another key consideration involves surface preparation before application. Thoroughly cleaning and decontaminating your vehicle's paint is essential for optimal results. Any residue left from previous waxes or sealants could prevent the coating from adhering properly. Ensuring that you eliminate all contaminants not only boosts bond strength but also minimizes unexpected delays in curing times.
Furthermore, let's not ignore the impact of post-application care.
After the initial application, how you treat your vehicle matters as well. Avoid washing your car or exposing it to heavy rain for at least 12-24 hours after applying ceramic coatings, since this initial period is critical for the proper curing process. Following the manufacturer's recommendations regarding wash routines and maintenance will either prolong or shorten the lifespan of your ceramic coat, ultimately affecting how well it performs its protective duties!
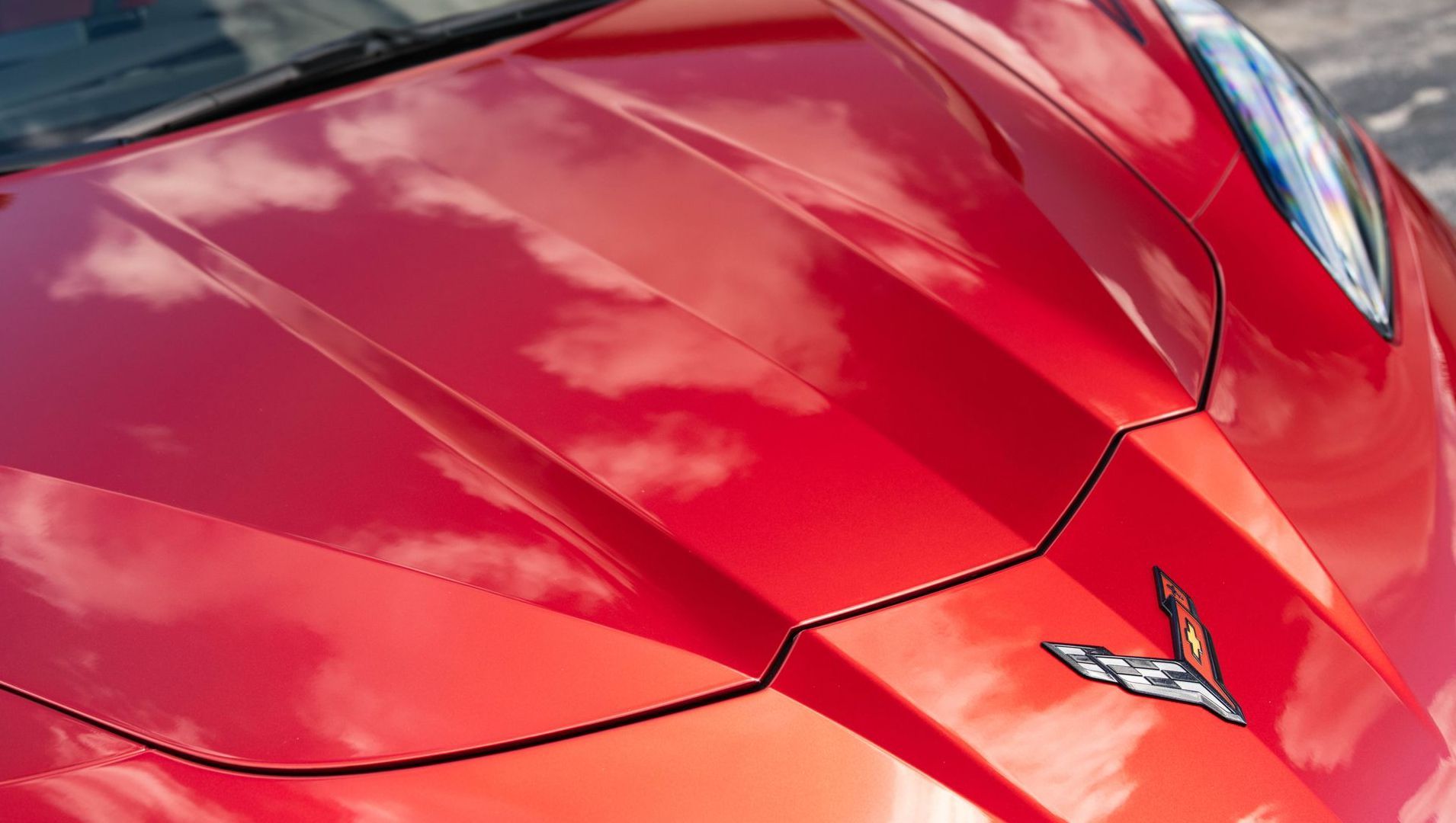
Environmental Conditions Impact
One of the most significant factors in the effectiveness of ceramic coatings is temperature.
Ideally, coatings cure best at temperatures between 60°F and 80°F (15°C - 27°C). Within this range, they have the perfect environment to allow the molecules within the coating to bond effectively, creating a robust protective layer on your vehicle's surface.
However, when the temperature dips below this threshold, several issues can arise. When it gets too cold, the curing process slows down dramatically, almost like trying to run through molasses. This sluggishness can lead to improper bonding and may leave the surface vulnerable to scratches and environmental contaminants.
Similarly, excessive heat can yield different complications by causing the coating to evaporate too rapidly while still curing, limiting its adhesion properties.
Just as critical as temperature is humidity; let’s dive into its effects.
Temperature and Humidity
Humidity plays a dual role in the curing of ceramic coatings. Ideally, you want low humidity levels—below 50% if possible. Low humidity allows for effective evaporation of solvents from the coating, leading to a quicker curing process. Conversely, high humidity can slow down evaporative processes, which might sound innocuous at first but leads to prolonged curing times, reducing effectiveness. Interestingly enough, though, high humidity can also accelerate certain chemical reactions within the coating itself if managed properly; this means that too much moisture can be a double-edged sword.
Beyond just keeping an eye on temperature and humidity during application, it's important to continue monitoring conditions afterward as well. For example, understanding your local climate will help you determine whether it’s advisable to apply new layers of coating based on weather forecasts. If rain is expected within 24 hours after application, you risk washing away any newly applied layers before they even have a chance to set and adhere.
Identifying Fully Cured Coatings
Knowing when your ceramic coating is fully cured is essential for ensuring that you're getting the most out of this advanced protective layer on your vehicle. The process may seem simple, but there are specific indicators to keep in mind that confirm both the integrity and effectiveness of the coating.
One primary method is the touch test; when you run your fingers across the surface, it should feel rigid rather than tacky. If it has a sticky texture, this could indicate incomplete curing, which affects its hydrophobic properties.
Next comes the all-important visual inspection. A successfully cured coating will have a high-gloss finish without any signs of hazing or cloudiness. This shiny veneer doesn’t just look good—it's a reflection of how well the coating has bonded to the paint beneath it. If you notice dullness or any irregularities, it’s worth reevaluating your application methods or considering a professional touch-up.
Achieving visual perfection isn't just cosmetic; it plays an instrumental role in maintaining your vehicle's appearance and longevity.
The water test is another tried-and-true method to assess whether your ceramic coating is fully cured. When you splash water on the surface, fully cured coatings will cause water to bead up tightly and roll off effortlessly, like small mercury droplets dancing upon the surface. Conversely, if you notice that water sheets rather than beads, it signifies that the coating may be losing its effectiveness.
These simple tests—touching, inspecting visually, and witnessing the hydrophobic reaction—are crucial, but attaining these outcomes requires optimal environmental conditions during and after application.
With just a few moments of tactile exploration and a couple of visual checks, you can confidently assess the curing status of your coating. Knowing your coating is fully cured helps maintain the luster and protection of your vehicle while driving through varied weather conditions.
For more detailed guides and product recommendations, visit our website at The Detail Doc.
By adopting these practices, you're not just investing in a product —you're investing in the longevity and beauty of your vehicle's appearance. If you have any questions or need further assistance, call us at (989) 244-0505.
The Detail Doc Blog
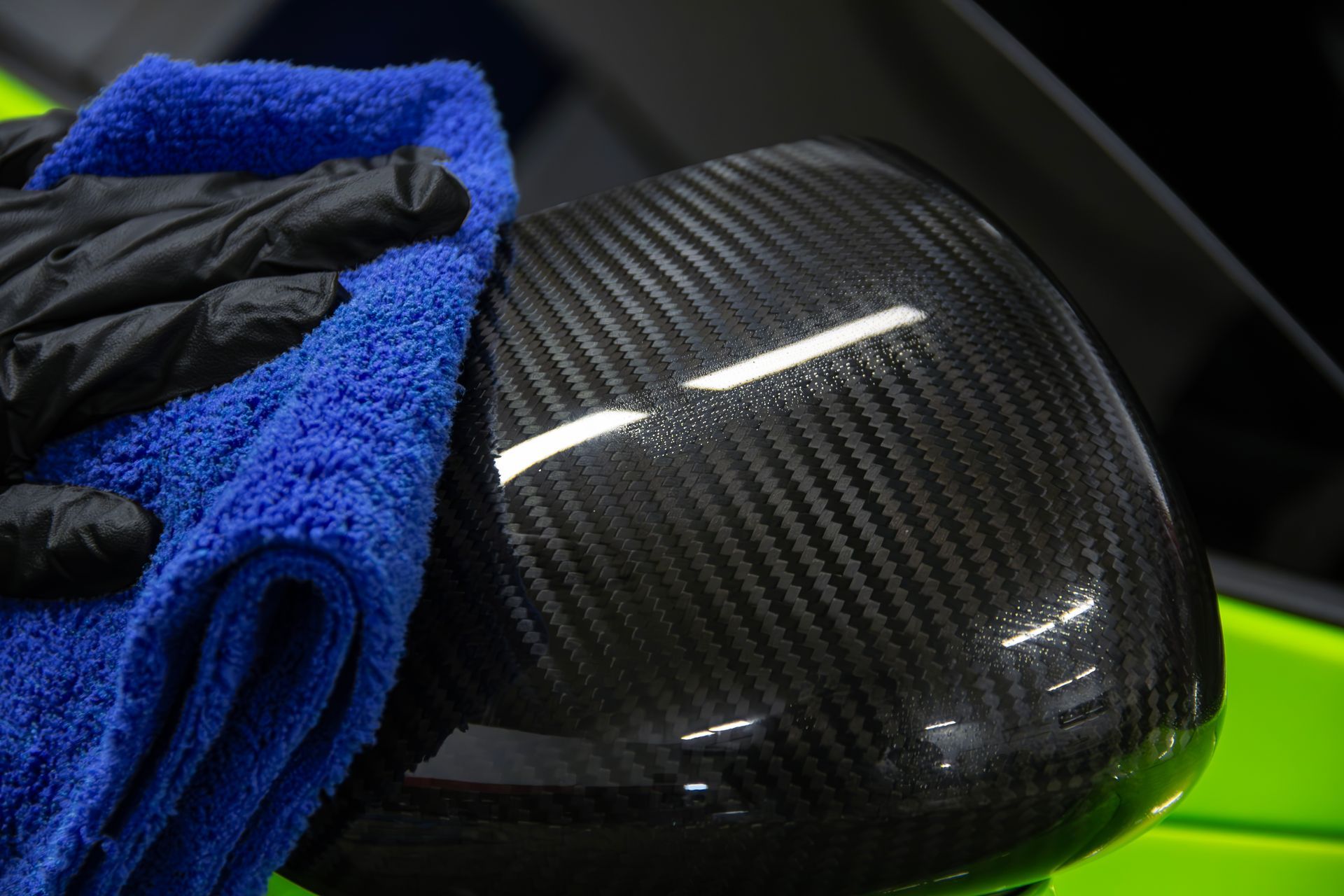